Mercaptans Removal
Mercaptans Removal
Equinox specializes in facility design and construction projects that deal with treatment of sour streams with varying levels of CO2 and H2S up to 40% concentration. We have installed over 50 of these facilities in Alberta, British Columbia and Manitoba while meeting all provincial regulatory and compliance requirements.
Equinox has extensive experience evaluating and selecting a Mercaptan Removal technology that is best fit-for-purpose based upon project specific criteria for:
- H2S, CO2 and Mercaptans Specifications
- Capital Costs
- Operating Costs
- Project Schedule
- Operability and Reliability
- Regulatory and Compliance Requirements
- Project Risks
Some of the companies and technologies include:
1. Nexo Solutions – Exion LT Liquid Treating System Design
The Exion LT Liquid Treating System Design involves the condensate passing through a filter before being injected with the chemical. The chemical injected condensate then feeds into a coalescer where the chemical reaction takes place converting the sulphur species into water soluble components. Wash water is added before the second coalescer to remove the water soluble components from the product. The waste wash water and the spent chemical are sent to separate tanks from the coalescers for truck out.
2. Merichem – Thiolex and Regen Technology
Thiolex extracts light mercaptans as well as small amounts of CO2 and H2S from condensate. The compounds react with an alkaline caustic solution to form sodium salts that are insoluble in the condensate.
The condensate first passes through a strainer to remove large solid particles. The condensate then enters the first stage contactor together with caustic solution. The contactor contains metallic fibers for better contacting between condensate and caustic solution. As the condensate and caustic flows through the contactor most of the mercaptan is converted to sodium mercaptides, which is soluble in the caustic solution. After the contactor the condensate enter the Thiolex vessel with a coalescer which separates out the caustic due to density difference between the condensate and the caustic. The caustic leaves the Thiolex vessel and goes to the caustic regeneration system. The condensate then flows to the second stage contactor and Thiolex vessel to repeat the above process.
The caustic regeneration removes the sodium mercaptides from the caustic by converting it into a disulfide oil. The caustic first goes through a heater to heat it up to 55°C and a catalyst is added. Once the catalyst is added the enters at the oxidizer tower and is mixed with air. As the caustic travels up the tower the sodium mercaptides are oxided to disulfide oils. The regenerated caustic is pumped back to the Thiolex contactor.
3. Merichem – Mericat Technology
The condensate first passes through a strainer to remove large solid particles. Once the condensate enters the Mericat system air is added before it enters the contactor. The contactor contains metallic fiber. As the condensate flows down the contactor, the mercaptan sulfur is converted to disulfide oil compounds. The disulfide oil is dissolved in the condensate. The caustic is regenerated by sodium mercaptide oxidation reaction and is recycled back to the top of the contactor using a pump. The condensate enters a phase separator which contains a coalescer pad to remove excess caustic.
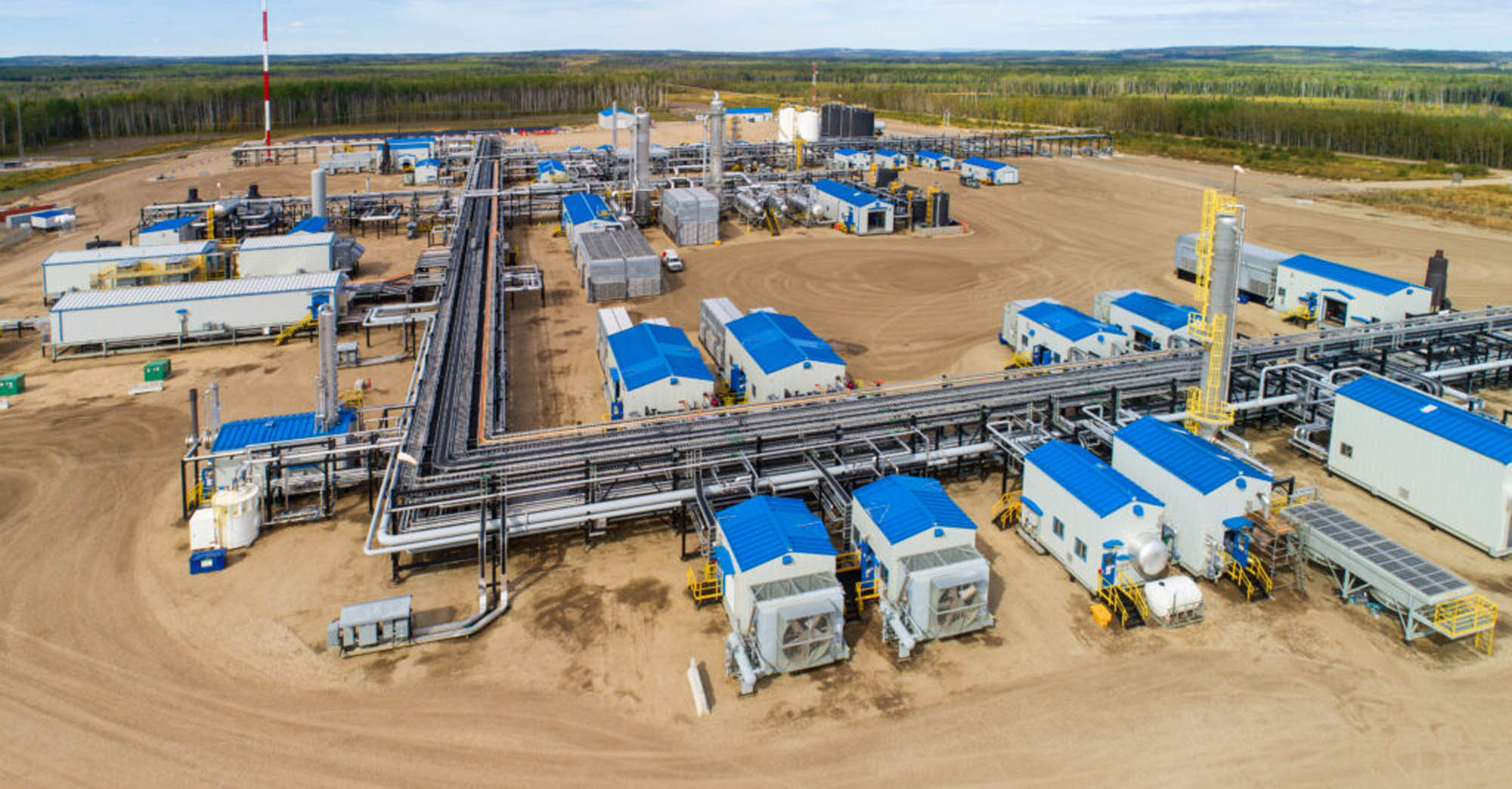
Recently commissioned 200 MMscfd gas processing facility with Mercaptans Removal